轴承检查和摩损测量
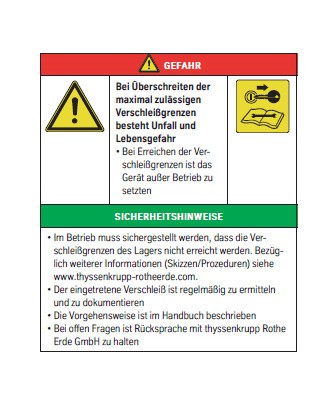
磨损极限安全提示
测量倾斜间隙
测量倾斜间隙
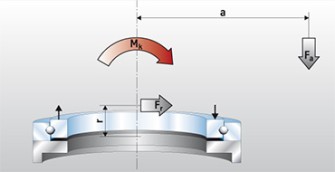
图 1:倾斜间隙测量的载荷原理(轴向运动)
如果可能,为确定磨损,我们推荐测量倾斜间隙。这种测量的载荷原理参见图 1。
在下部连接结构和与上部结构旋接在一起的轴承环之间(图 2)测得。这时为了尽量减少连接结构弹性变形的影响,必须尽可能在轴承的运行系统附近测量。
轴承检查 - 预防损坏
磨损测量可以在造成设备非计划性停机前提前发现技术问题。这样可以避免不必要的维修成本和昂贵的生产停顿。因此为了评估轴承状态,我们推荐定期测量轴承磨损。
通过轴向运动或下沉的变化,可以识别运行系统的磨损。根据使用情况或轴承规格的不同,可以通过测量倾斜间隙或下沉测量确定磨损增加。
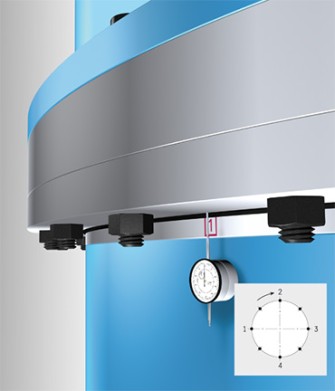
图 1:倾斜间隙测量的载荷原理(轴向运动)
方法的执行
- 在调试时进行基准测量。
- 从规定的位置标记圆周上的测量点。
- 在对测量精度为 0.01 mm 的量规进行零点调整时,首先要施加最高逆转力矩。之后——酌情通过承受负荷——产生向前倾翻的力矩。
- 在上部结构旋转之后,在标记的位置重新测量(参见表 4)。
轴承间隙允许的最大扩大幅度(均匀磨损)
重要:对于特殊的使用情况(与 thyssenkrupp rothe erde 协商),不允许扩大轴承间隙。这涉及用于 50% 列示值的运行工况的大型回转支承等。
表 1:BF* 01, 08(双列球轴承/推力球轴承)
测量方法 | 球体直径 (mm) | ||||||||||
---|---|---|---|---|---|---|---|---|---|---|---|
18 | 20 | 22 | 25 | 30 | 35 | 40 | 45 | 50 | 60 | 70 | |
允许的最高磨损值,最高 mm | |||||||||||
下沉测量 | 1.6 | 2.2 | 3.0 | 3.8 | |||||||
倾斜间隙测量 | 2.5 | 3.0 | 4.0 | 5.0 |
表 2:BF* 06, 09, 25, 23, 28(球轴承/成型支承)
测量方法 | 球体直径 (mm) | ||||||||||
---|---|---|---|---|---|---|---|---|---|---|---|
20 | 22 | 25 | 30 | 35 | 40 | 45 | 50 | 60 | 70 | ||
允许的最高磨损值,最高 mm | |||||||||||
下沉测量 | 1.6 | 2.0 | 2.6 | 3.3 | |||||||
倾斜间隙测量 | 2.0 | 2.6 | 3.2 | 4.0 |
表 3:BF* 12, 13, 19(滚子回转支承
测量方法 | 球体直径 (mm) | |||||||||||||
---|---|---|---|---|---|---|---|---|---|---|---|---|---|---|
16 | 20 | 25 | 28 | 32 | 36 | 40 | 45 | 50 | 60 | 70 | 80 | 90 | 100 | |
允许的最高磨损值,最高 mm | ||||||||||||||
下沉测量 | 0.8 | 1.2 | 1.6 | 2.0 | 2.4 | |||||||||
倾斜间隙测量 | 1.4 | 2.0 | 2.8 | 3.5 | 4.2 |
表 1:BF* 01, 08(双列球轴承/推力球轴承)
测量方法 | 球体直径 (mm) | ||||||||||
---|---|---|---|---|---|---|---|---|---|---|---|
18 | 20 | 22 | 25 | 30 | 35 | 40 | 45 | 50 | 60 | 70 | |
允许的最高磨损值,最高 mm | |||||||||||
下沉测量 | 1.6 | 2.2 | 3.0 | 3.8 | |||||||
倾斜间隙测量 | 2.5 | 3.0 | 4.0 | 5.0 |
表 1:BF* 01, 08(双列球轴承/推力球轴承)
测量方法 | 球体直径 (mm) | ||||||||||
---|---|---|---|---|---|---|---|---|---|---|---|
18 | 20 | 22 | 25 | 30 | 35 | 40 | 45 | 50 | 60 | 70 | |
允许的最高磨损值,最高 mm | |||||||||||
下沉测量 | 1.6 | 2.2 | 3.0 | 3.8 | |||||||
倾斜间隙测量 | 2.5 | 3.0 | 4.0 | 5.0 |
表 2:BF* 06, 09, 25, 23, 28(球轴承/成型支承)
测量方法 | 球体直径 (mm) | ||||||||||
---|---|---|---|---|---|---|---|---|---|---|---|
20 | 22 | 25 | 30 | 35 | 40 | 45 | 50 | 60 | 70 | ||
允许的最高磨损值,最高 mm | |||||||||||
下沉测量 | 1.6 | 2.2 | 2.6 | 3.3 | |||||||
倾斜间隙测量 | 2.0 | 2.6 | 3.2 | 4.0 |
表 2:BF* 06, 09, 25, 23, 28(球轴承/成型支承)
测量方法 | 球体直径 (mm) | ||||||||||
---|---|---|---|---|---|---|---|---|---|---|---|
20 | 22 | 25 | 30 | 35 | 40 | 45 | 50 | 60 | 70 | ||
允许的最高磨损值,最高 mm | |||||||||||
下沉测量 | 1.6 | 2.2 | 2.6 | 3.3 | |||||||
倾斜间隙测量 | 2.0 | 2.6 | 3.2 | 4.0 |
表 3:BF* 12, 13, 19(滚子回转支承)
测量方法 | 球体直径 (mm) | |||||||||||||
---|---|---|---|---|---|---|---|---|---|---|---|---|---|---|
16 | 20 | 25 | 28 | 32 | 36 | 40 | 45 | 50 | 60 | 70 | 80 | 90 | 100 | |
允许的最高磨损值,最高 mm | ||||||||||||||
下沉测量 | 0.8 | 1.2 | 1.6 | 2.0 | 2.4 | |||||||||
倾斜间隙测量 | 1.4 | 2.0 | 2.8 | 3.5 | 4.2 |
表 3:BF* 12, 13, 19(滚子回转支承)
测量方法 | 球体直径 (mm) | |||||||||||||
---|---|---|---|---|---|---|---|---|---|---|---|---|---|---|
16 | 20 | 25 | 28 | 32 | 36 | 40 | 45 | 50 | 60 | 70 | 80 | 90 | 100 | |
允许的最高磨损值,最高 mm | ||||||||||||||
下沉测量 | 0.8 | 1.2 | 1.6 | 2.0 | 2.4 | |||||||||
倾斜间隙测量 | 1.4 | 2.0 | 2.8 | 3.5 | 4.2 |
检查轮齿
检查轮齿
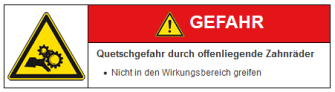
挤伤危险安全提示
在使用寿命期间,出现磨合平整和轮齿磨损。允许的磨损极限值与使用情况密切相关。根据经验,允许的磨损最高可达 0.1 x 各齿面的模数。
下沉测量
下沉测量
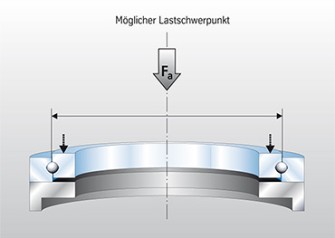
图 3:下沉测量的载荷原理
我们推荐在无法测量倾斜间隙的位置进行下沉测量。这时载荷组合的重心位于轴承的转弯直径内。在图 3 中展示载荷原理。
在下部连接结构和与上部结构旋接在一起的轴承环之间(图 4,5)测得。
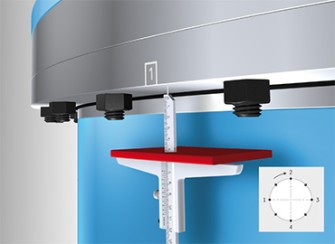
图 4:使用游标深度尺进行下沉测量的原理结构
流程与测量倾斜间隙类似:
- 在调试设备时确定基准值。
- 从规定的位置标记圆周上的测量点。
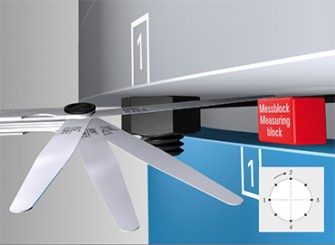
图 5:使用量规进行下沉测量的原理结构
在检查完轴承固定螺栓之后,应以恰当的时间间隔在相同的条件下重新进行倾斜间隙和下沉测量。与基准测量的相应差异说明了在此期间出现的磨损。在磨损值升高时,应缩短测量间隔时间。
优点: 通过明确评估轴承状态可以及时更换已磨损的零件。因此与最佳的备件管理一起,可以避免损坏情况和长时间停机。
提示: 如果超过允许的磨损值,我们推荐停止设备。
可选方案:集成磨损测量装置 (IWM)
为了继续优化设备的功能和运行安全性,thyssenkrupp rothe erde 不间断地开发用于持续监控状态的创新解决方案。为大型回转支承所集成的磨损测量装置是一项已经申请专利的发明。它可以在线检查允许的最大轴隙或回转支承的下沉。
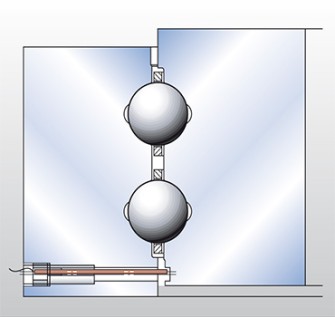
图 6:测量球轴承中的磨损
优点: 不需要中断运行以检测轴隙。
在滚道的峰值载荷区域内有一枚不锈钢探针。它——电绝缘——安装在一个环件中。探针顶入对置环中的凹槽。可以通过槽宽设置允许的最大间隙。
如果间隙变化过大,对置环会与探针发生接触。在探针接触对置环时,通过探针的电气连接释放一个信号。该信号表示已达到对置环的允许相对偏移,需要检查轴承。
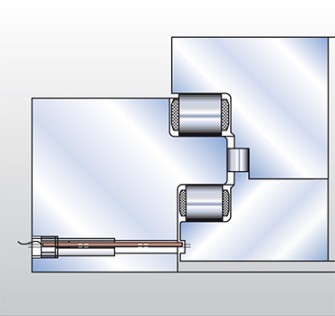
图 7:测量滚子轴承中的磨损
优点: 连接结构的变形和螺栓连接的弹性对测量结果的影响并不明显。
滚道的弹性接近量、轴承的轴向间隙和接触面的平整度偏差得到补偿。最大化降低保养人员的成本。
润滑脂试样提取
润滑脂试样提取
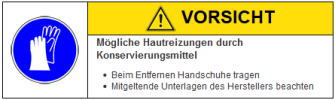
对于防腐剂可能刺激皮肤的警告提示
润滑脂试样提取套件
润滑脂试样提取套件
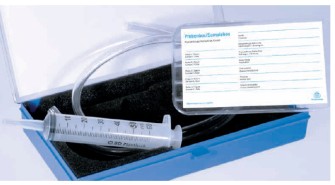
图 8:润滑脂试样提取套件
与检查测量的同时,提取使用过的润滑脂的试样。分析使用过的润滑脂可以了解有关滚道状态的详细信息。
带润滑脂取样孔的轴承
带润滑脂取样孔的轴承
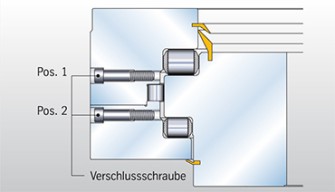
图 9:带润滑脂取样孔的三列滚子回转支承
润滑脂试样提取套件由一根塑料软管、若干塞盖、一个抽取装置和一个最多可放置五份润滑脂试样的试样盒,以及一张信息表组成。详细说明操作方法。
必须从主载荷区域中提取润滑脂试样。
去除为取样所选择的螺丝堵 (M16 EN ISO 4762)(图 9 和 10:位置 1,必要时在相对面,位置 2)。
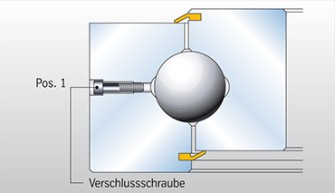
图 10:带润滑脂取样孔的单列球轴承
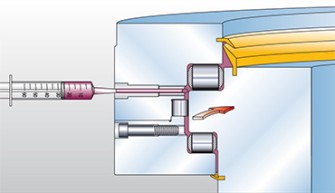
图 11:取样
在取出润滑脂试样之前,要斜切 (45°) 所提供的软管,其略长于润滑脂取样孔的总长度。将软管引入滚道区域中的相应钻孔(图 11)。
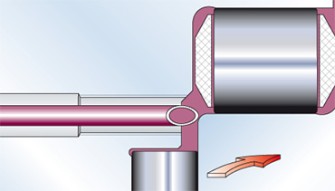
图 12:取样的详细概要图
这时必须与旋转方向相反定位 45° 的切割面(图 12)。
使用螺丝堵重新封闭取样孔。
在提取完润滑脂之后,用塑料盖封闭软管的两端。
对润滑脂试样编号,放入已标识的试样盒中。
在上方为试样盒添加必要的信息(参见润滑脂试样提取套件,图 8)。
不带润滑脂取样孔的轴承
不带润滑脂取样孔的轴承
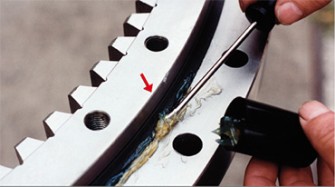
图 13:在密封唇上提取润滑脂
如果在轴承上未设置润滑脂取样孔,在密封垫上提取一个或多个润滑脂试样。在润滑嘴附近清洁该区域。优先在主工作区内和/或错位 180° 取样。
在上述润滑嘴(不旋转轴承)上补充润滑时,取出密封唇上溢出的第一份润滑脂。提取量为 3 ccm 即可。
提示: 请注意认真取样,否则会因污染造成结果畸变。
Fe 极限值
Fe 极限值
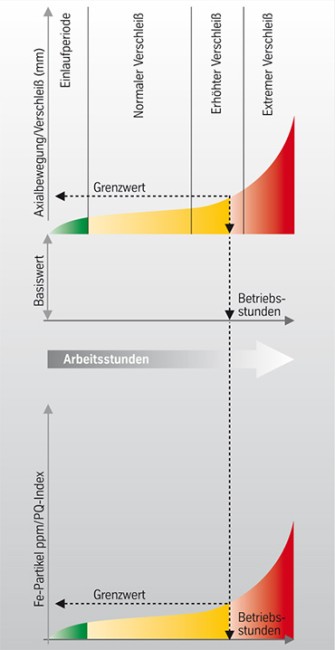
图 14:磨损曲线
润滑剂许可的 Fe 污染极限值主要取决于运行参数和再润滑间隔时间。根据使用情况的不同,该数值最高可达 20000 ppm。
磨损曲线
图表显示了与运行小时数有关的磨损增加,或 Fe 颗粒和 PQ 指数增加(图 14)。
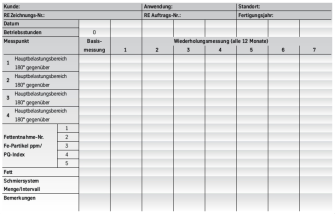
表 4:测量表格
点击这里放大
标准使用情况参见表 1-3 中的值。在达到极限值时,请联系 thyssenkrupp rothe erde。
应将测量值和分析值以及轴承专用信息填入单独的表格中(参见表 4),并提供给 thyssenkrupp rothe erde。请将试样盒发送至 thyssenkrupp rothe erde。
thyssenkrupp Rothe Erde GmbH
Service
Beckumer Straße 87
59555 Lippstadt
service.rotheerde@thyssenkrupp.com
thyssenkrupp rothe erde 将润滑脂试样发送至经审核、有资质的试验室。
优点: 处理时间短,通过电子邮件提供有关分析结果以及磨损测量的信息。
请向以下地址索要润滑脂试样提取套件 :
thyssenkrupp Rothe Erde GmbH
Tremoniastraße 5-11
44137 Dortmund
电话 (02 31) 186-0
传真 (02 31) 186-2500
sales.rotheerde@thyssenkrupp.com